Unlocking the Power of 80/20 Fasteners: A Comprehensive Guide
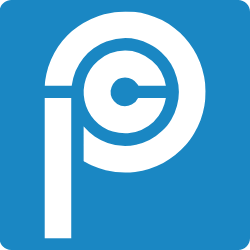
Milan Lakhani
CPI Automation Team
Date of publication
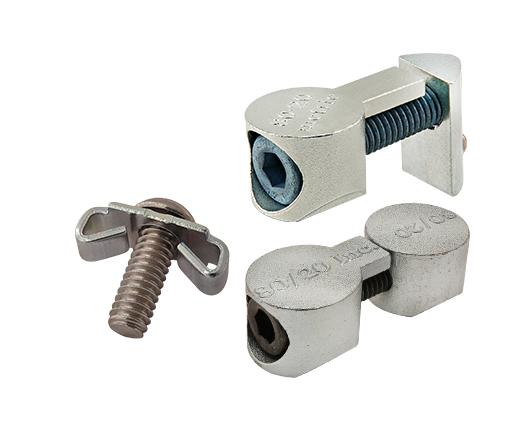
Welcome to CPI Automation Ltd insightful journey into the world of 80/20 fasteners and their compatibility with 80/20 aluminum extrusions. Whether you're a seasoned engineer, a passionate DIY enthusiast, or someone embarking on their very first project, this blog is your go-to resource for harnessing the incredible potential of 80/20 fasteners.
What to Expect
In this guide, we'll cover it all:
- Understanding 80/20 Fasteners: Learn the basics of these building blocks, essential for any project.
- Types of Fastening Methods and Fasteners: Discover various fastener types and real-world applications.
- Selecting the Right Fastener: Make informed choices for projects like DIY, truck/RV upgrades, and gaming setups.
Section 1: Understanding 80/20 Fasteners
In the world of structural connections, where precision and versatility matter most, 80/20 fasteners are the unsung heroes. At CPI Automation Ltd, we believe that to harness their potential fully, you must first understand what these fasteners are and how they shape the world of aluminum extrusion projects.
What are 80/20 Fasteners?
80/20 fasteners are specialized components designed to securely connect and fasten various parts of aluminum extrusions in a modular framing system. They play a pivotal role in the assembly of structures, allowing for the creation of anything from workstations to shelving units and elaborate industrial machinery. These fasteners are tailored to fit perfectly within the T-slot channels of 80/20 aluminum extrusions, offering a versatile and reliable solution for building robust structures.
Internal vs. External Fasteners
80/20 fasteners can be broadly categorized into two types: internal and external fasteners. Each type has its advantages and disadvantages, making them suitable for different applications.
Internal Fasteners:
- Advantages: Internal fasteners, like anchor fasteners and end fasteners, are discreet and hidden within the T-slot channel, providing a sleek and clean appearance. They are excellent for applications where aesthetics matter.
- Examples: Anchor fasteners securely anchor components to the T-slot. End fasteners are used to close off the end of an extrusion.
External Fasteners:
- Advantages: External fasteners, including brackets, joining plates, and 45-degree supports, are versatile and easy to access. They offer flexibility and accessibility when making adjustments or modifications to your structure.
- Examples: Brackets provide additional support and attachment points. Joining plates connect two extrusions at right angles. 45-degree supports offer diagonal bracing for added stability.
Choosing the Right Type:
Selecting between internal and external fasteners depends on your specific project requirements. For aesthetic projects like furniture or retail displays, internal fasteners may be the preferred choice. On the other hand, when flexibility and accessibility are paramount, external fasteners shine. For example, if you're building an adjustable workstation, external brackets and joining plates make adjustments a breeze.
In essence, 80/20 fasteners are the glue that holds your aluminum extrusion projects together, and understanding the distinction between internal and external types empowers you to craft structures that are both functional and visually appealing. As we delve deeper into this guide, you'll discover how to make informed choices based on your unique project needs.
Section 2: Types of Fastening Methods and Fasteners
Fastening methods in the world of 80/20 aluminum extrusions are as diverse as the projects they support. In this section, we will explore a variety of fastener types and provide real-world examples of how each type can be used to bring your creations to life.
1. T-Nuts:
Description: T-nuts are a fundamental and widely used type of fastener in the 80/20 system. They slide into the T-slot channels of the extrusions and provide a threaded connection for bolts.
Real-World Application: Imagine assembling a sturdy workbench frame. T-nuts are used to secure the legs to the frame while allowing for easy height adjustments.
2. Corner Brackets:
Description: Corner brackets, as the name suggests, are used to create right-angle connections between extrusions. They are available in various sizes and angles to suit your needs.
Real-World Application: When building a custom shelving unit, corner brackets are indispensable for creating stable, square corners.
3. Anchor Fasteners:
Description: Anchor fasteners are internal fasteners designed to securely anchor components within the T-slot channel. They are ideal for discrete connections.
Real-World Application: In the construction of a mobile workstation, anchor fasteners hold the tabletop securely to the frame without protruding externally.
4. Joining Plates:
Description: Joining plates provide a flat surface for connecting two extrusions at right angles. They offer stability and flexibility in creating strong connections.
Real-World Application: When designing a modular industrial workbench, joining plates ensure a robust connection between the frame and the work surface.
5. Hinge Assemblies:
Description: Hinge assemblies allow for the creation of hinged doors, lids, or panels within your aluminum extrusion structures. They enable easy access and movement.
Real-World Application: Designing an electronics enclosure? Hinge assemblies facilitate the creation of access panels for maintenance and equipment installation.
These are just a few examples of the diverse fastening methods and fasteners available in the 80/20 system. Each type serves a unique purpose, enabling you to construct everything from workstations and industrial equipment to custom furniture and display systems. As you embark on your projects, consider the specific requirements and functions of these fasteners to make your creations not only functional but also efficient and visually appealing. In the following sections, we'll delve deeper into how to choose the right fastener for your specific needs and explore their compatibility with different 80/20 aluminum extrusions.
Section 3: How to Select the Right Fastener for Your Project
No more guesswork! We're here to help you navigate the maze of 80/20 fasteners and ensure you choose the perfect one for your specific project. Imagine the confidence of knowing you've selected the ideal fastener whether you're embarking on a DIY furniture project, upgrading your truck/RV, setting up a gaming paradise, or working on an industrial assembly. Let's break down the decision-making process step by step:
1. Define Your Project's Objectives:
Start by clearly defining the goals and objectives of your project. What are you trying to achieve, and what functionality or features do you need? For instance, are you building a sturdy workbench, enhancing the storage capacity of your truck, or creating a custom gaming rig? The objectives will guide your fastener selection.
2. Consider Load Requirements
Determine the load-bearing requirements of your project. How much weight will the structure need to support? This is a critical factor in choosing fasteners that can handle the expected loads without compromising safety and stability.
3. Material Compatibility:
Ensure that the materials used in your project are compatible with the chosen fasteners. Different materials may require specific types of fasteners to ensure a secure and lasting connection. For example, consider the compatibility of fasteners with both aluminum extrusions and the materials you intend to attach.
4. Aesthetics Matter:
If your project's appearance is a key consideration, think about how the fasteners will affect the overall look. Internal fasteners like anchor fasteners can provide a sleek and unobtrusive finish, ideal for furniture or displays. External fasteners may offer a more industrial appearance but are often preferred for accessibility.
5. Flexibility and Adjustability:
Consider whether you need flexibility and adjustability in your project. Some fasteners, like T-nuts and corner brackets, allow for easy modifications and reconfigurations, which can be invaluable in projects that may evolve over time.
6. Consult Manufacturer Guidelines:
Always refer to the manufacturer's guidelines and recommendations for fastener selection. 80/20 suppliers often provide detailed information on which fasteners work best with their extrusions, helping you make informed choices.
By following these steps, you can make informed decisions and confidently select the right fastener for your project. Whether you're aiming for functional perfection in an industrial setting or seeking aesthetic harmony in your DIY creations, understanding your project's specific needs is the first step toward success. In the next section, we'll explore the compatibility of different 80/20 aluminum extrusions with various fasteners, providing you with practical examples to further guide your selection process.
Here’s an Example to better understand how to select the right fastener for your project:
The Adjustable Workbench
Imagine you're setting up a workshop, and at the heart of it, you want an adjustable workbench. This workbench should not only be rock-solid but also allow for easy customization and reconfiguration as your projects evolve. Choosing the right fastener for this project was crucial for its functionality and versatility.
Project Requirements:
- Stability and Strength: The workbench needed to support heavy tools and materials without wobbling or sagging.
- Adjustability: To accommodate different tasks and projects, the workbench had to be adjustable in height and width.
- Modularity: The ability to attach additional accessories and shelves as needed for various projects.
Clean Aesthetic: As it would be a central piece in the workshop, an industrial, clean aesthetic was desirable
The Right Fastener Choice: T-Nuts and Corner Brackets
For this project, the selection of fasteners played a pivotal role in achieving all the desired outcomes:
T-Nuts: These fasteners allowed for height adjustability by sliding within the T-slot channels of the aluminum extrusions that formed the legs of the workbench. Bolts inserted through the T-nuts secured the legs to the frame, ensuring stability.
Corner Brackets: To create a robust and square frame for the workbench, corner brackets were used at each corner junction. They ensured the workbench's stability and strength, even when heavy loads were placed on it.
The choice of these fasteners transformed a simple workbench into a dynamic and indispensable tool in the workshop. It showcased how the right fastener selection can make a significant difference in project success, enabling versatility, strength, and aesthetics in one harmonious package. This case study underscores the importance of understanding your project's specific requirements when choosing fasteners and how they can elevate the functionality and usability of your creations.
Conclusion
In conclusion, 80/20 fasteners are the keys to unlocking your project's potential. With a firm grasp of their types, applications, and compatibility with diverse aluminum extrusions, you now possess the confidence to turn your ideas into reality. These versatile connectors empower engineers, DIY enthusiasts, and creators of all kinds to build with precision and creativity. So, go ahead and embark on your projects with the assurance that you can craft sturdy, functional, and aesthetically pleasing structures. The world of 80/20 fasteners is yours to explore and conquer.
Milan Lakhani
CPI Automation Team
Want to buy these 80/20 Products Online?
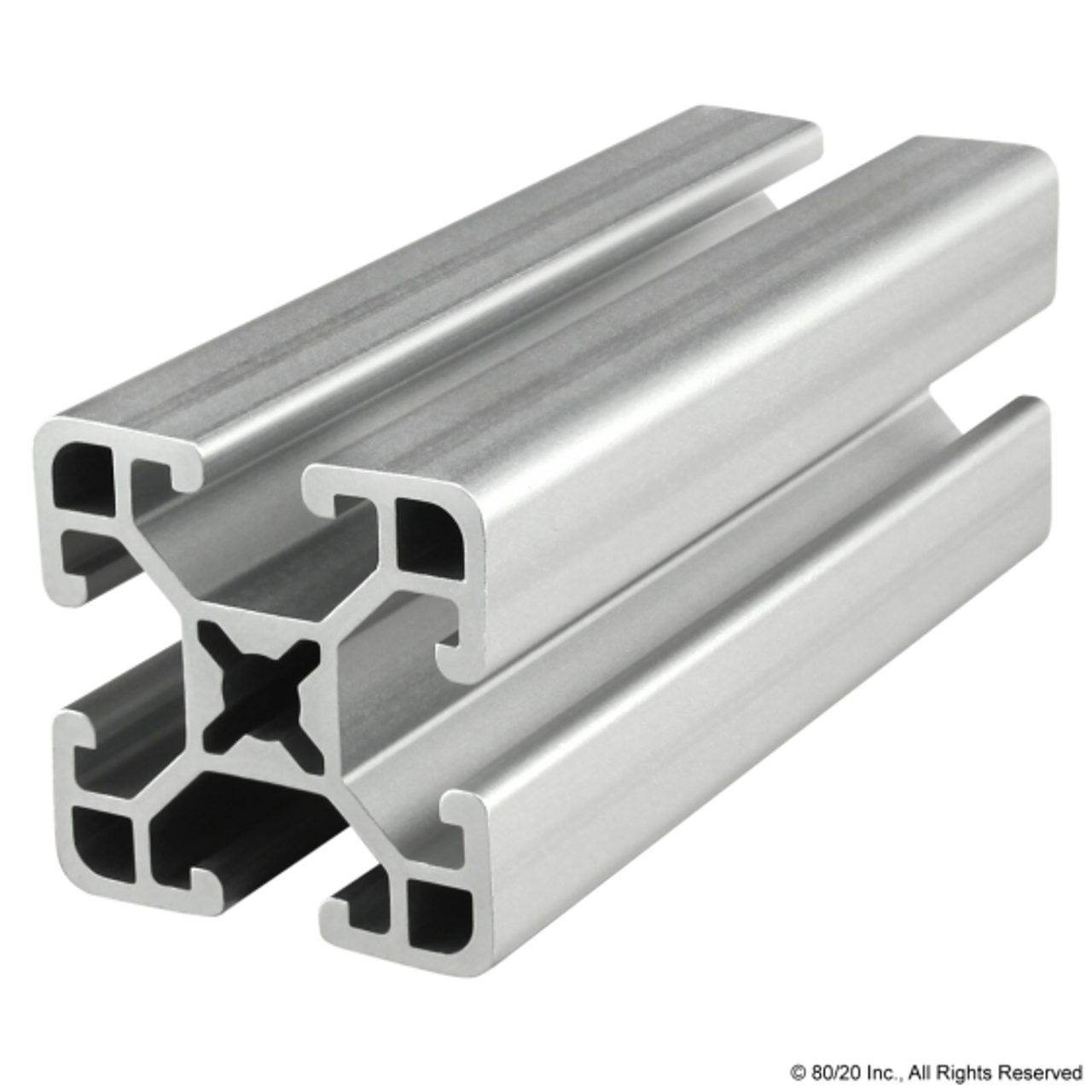
1.50" X 1.50" Ultra-Lite Smooth Surface T-Slotted Profile - Four Open T-Slots
CAD $3.82
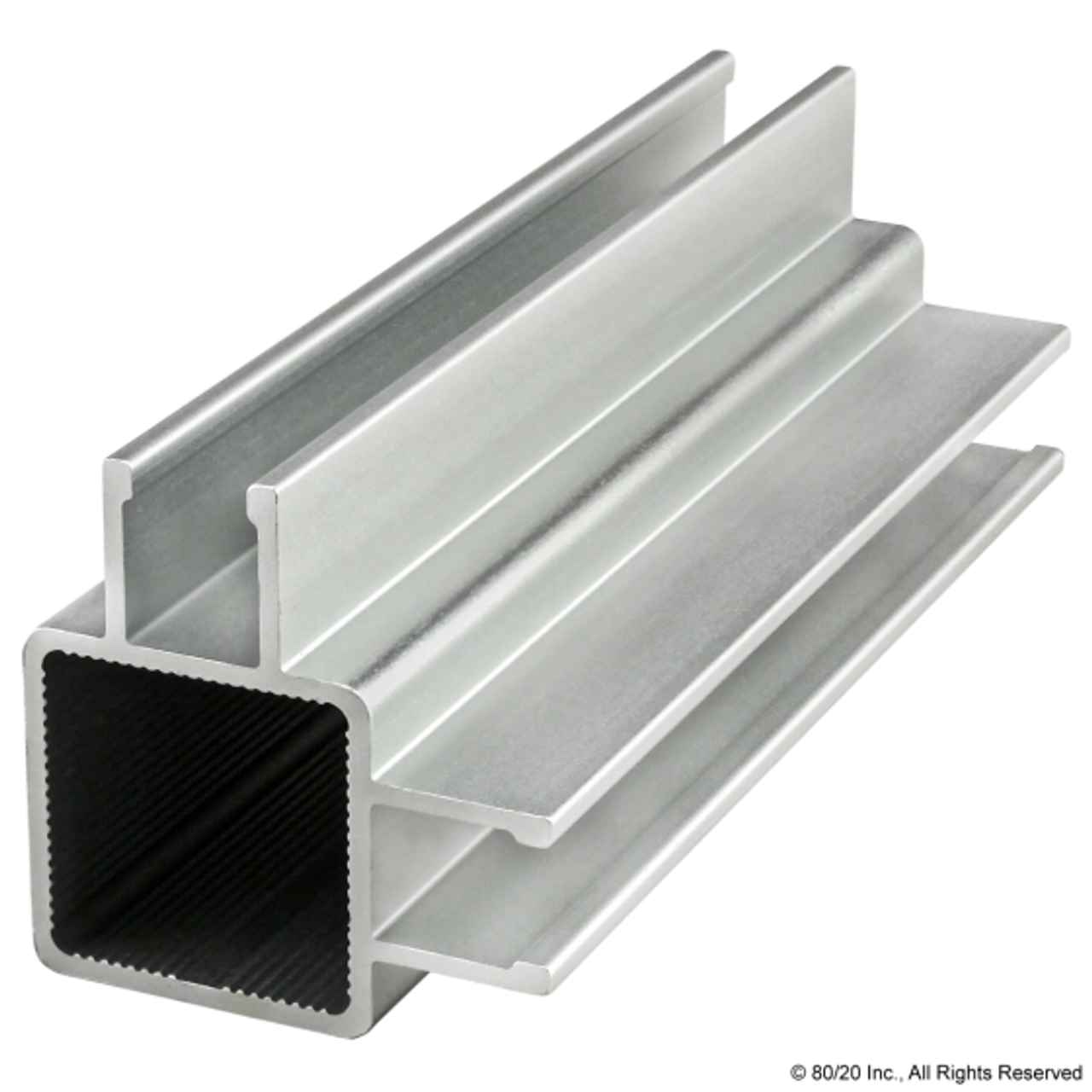
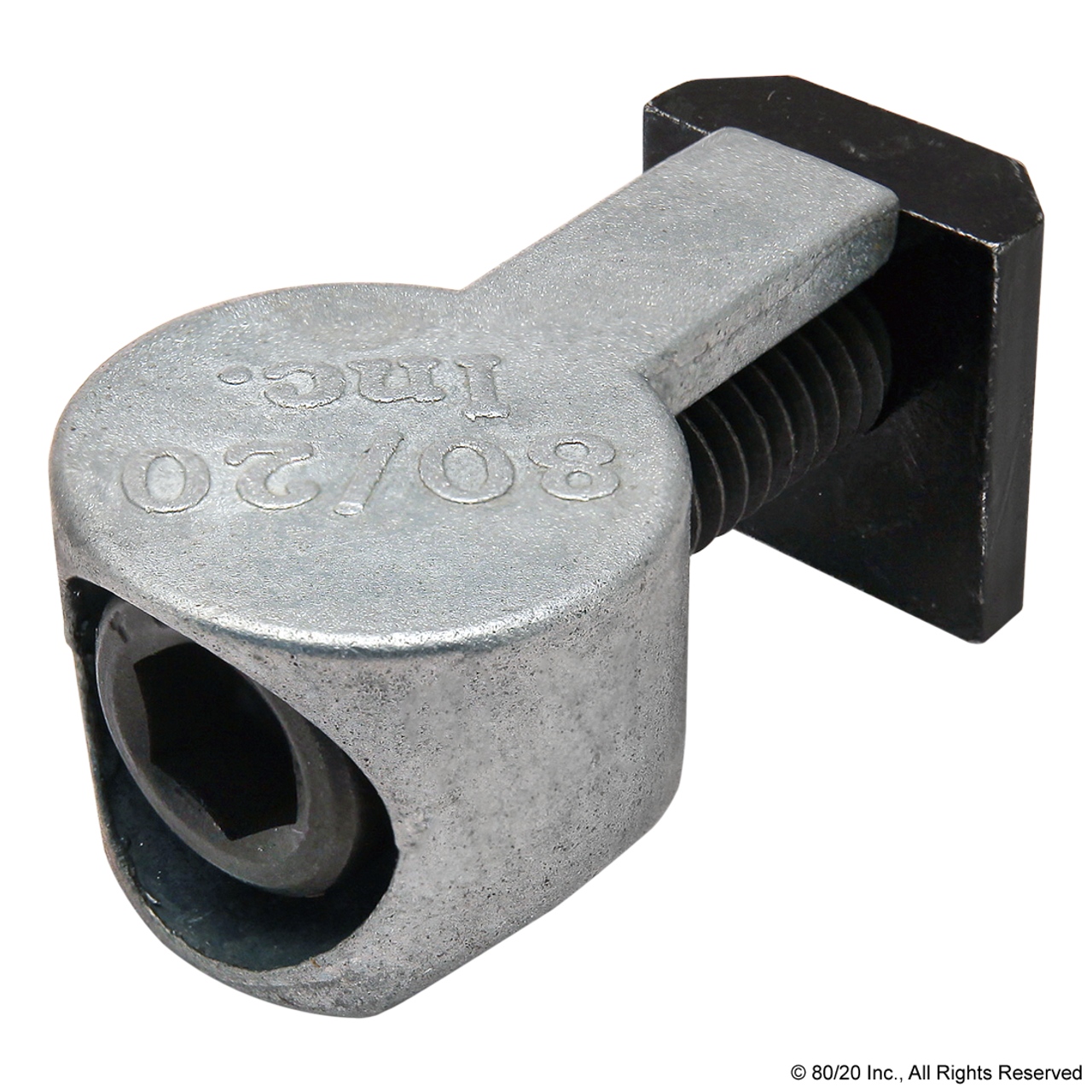